Asphalt vs. Gravel Truck Parking Surface Types: The Surprising #1 Factor That Drives Truck Parking Demand
Introduction
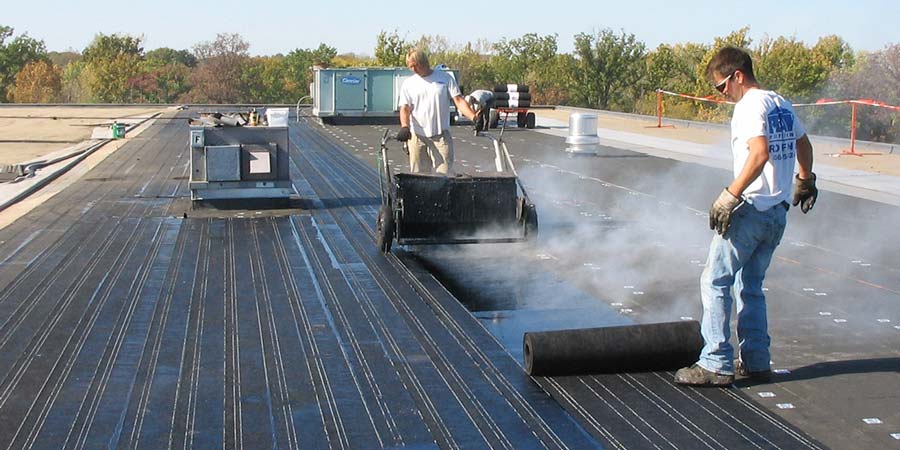
When it comes to attracting and retaining truck drivers, the parking surface type can make all the difference. While factors like location, pricing, and security are certainly important, the actual surface material used in a truck parking facility is often the overlooked #1 priority for drivers.
In this blog post, we’ll explore the key differences between the two most common parking surfaces – asphalt and gravel – and why one consistently outperforms the other when it comes to driver satisfaction and occupancy rates.
The Asphalt Advantage – and what to watch out for!
Asphalt-paved truck parking lots offer a number of advantages that make them the preferred choice for many drivers:
Defined, Striped Spaces: Asphalt surfaces allow for clear delineation of individual parking spots through the use of painted lines and numbering. This organization makes it easy for drivers to identify and maneuver into their assigned spaces.
Smooth, Level Surface: Asphalt provides a consistently flat, even surface that is simple for trucks to drive on and park. Drivers don’t have to worry about uneven ground or the risk of getting stuck, as can happen on gravel lots.
Easier Maneuverability: The smooth, defined spaces of an asphalt lot enable drivers to smoothly enter, exit, and reposition their vehicles as needed. This improves traffic flow and reduces the frustration of navigating a chaotic parking environment.
Perception of Security and Professionalism: Asphalt-paved lots are often viewed by drivers as more secure, well-maintained, and professionally operated facilities. This perception can be an important factor in attracting and retaining customers.
The Gravel Drawbacks – with some truck parking pros
In comparison, truck parking lots with a gravel or compacted aggregate surface tend to present more challenges for drivers:
Undefined, Uneven Spaces: Without clear striping or delineation, gravel lots force drivers to guess at proper parking alignment and placement. The uneven ground can also make it difficult to maneuver and park safely.
Potential for Getting Stuck: The loose, shifting nature of gravel surfaces increases the risk of truck tires becoming stuck or bogged down, especially in wet conditions. This can lead to frustration and the need for assistance to get moving again.
Harder to Navigate: Navigating a gravel lot requires more caution and skill from drivers, as the surface is less forgiving of wide turns or sudden movements. This can slow down traffic flow and create a more stressful parking experience.
Perceived as Less Secure: Gravel lots often give the impression of a less professional, less well-maintained operation. Drivers may feel their vehicles and cargo are less secure in these types of facilities.
Truck Parking’s Real-World Comparison
To illustrate the real-world impact of parking surface type, consider this case study of two similar truck parking lots:
Lot A: Asphalt-paved, with clearly marked and numbered spaces. Located in a prime industrial area, with competitive pricing and security measures in place.
Lot B: Gravel surface, with no defined parking layout or organization. Similar location and pricing to Lot A, but without the same security features.
Despite the similarities in other key factors, Lot A consistently maintained significantly higher occupancy rates compared to Lot B. Drivers overwhelmingly preferred the smoother, more organized asphalt surface, even if it meant paying a slightly higher price.
Interviews with the drivers revealed that the parking surface type was the primary determining factor in their decision-making process. Other considerations, such as location and cost, were secondary to the practical and psychological benefits of an asphalt-paved lot.
The Cost of Building a Truck Parking Facility
One of the most common questions we field at Rig Hut Truck Parking is: “What is the cost of building a truck parking facility?” To get a clearer idea, let’s explore a significant part of your budget: the cost of fill material. More on this can be found here: https://blog.therighut.com/2023/09/04/cost-of-building-a-truck-parking-facility-understanding-fill-material-costs/
The Need for Fill in Truck Parking Facilities
When planning a truck parking facility, layout and design take center stage. For design tips, our earlier blog “Truck Parking Optimization with Rig Hut” is a valuable resource. Before diving into design, you’ll need to prepare the land. That’s where the cost of fill material comes into play.
Units and Measurements: Breaking it Down
Fill material usually gets quoted per “load,” essentially a dump truck full. Elevation gets measured in feet, and you calculate the volume of earth needed in cubic yards (Length x Width x Height).
Acre-Foot: The Standard Unit for Elevation
An acre-foot represents the volume required to raise one acre by one foot in elevation. This is about 1,613 cubic yards.
Load Calculations: How Much Fill Do You Need?
To elevate an acre by one foot, you’d typically need around 90 loads of fill. The math is simple: divide 1,613 cubic yards in an acre-foot by 18 cubic yards per load.
Note: Keep in mind that this calculation doesn’t include compaction, which might require additional fill material.
Costs per Load: What Should You Expect?
The cost varies by material type and the surface you intend to create. For more on surfaces, consult our “Ultimate Guide to Truck Parking Surfaces.” To get a precise estimate, it’s best to call a local contractor.
Bringing it All Together: Estimating Costs
To estimate the cost of fill material, you’ll need three crucial pieces of information: your site’s current elevation, any required scraping, and your municipality’s required elevation for truck parking.
For those interested in renting out unused yard space, our Rig Hut Marketplace is an excellent solution. Learn how to generate additional income via our “Rent My Yard” feature.
Balancing Costs and Benefits
When weighing the decision between asphalt and gravel for your truck parking facility, it’s important to consider both the initial construction costs and the long-term operational implications.
Asphalt surfaces generally require a higher upfront investment compared to gravel. However, the benefits of improved driver satisfaction, higher occupancy rates, and reduced maintenance needs can make the additional cost worthwhile in the long run.
Gravel lots may be less expensive to construct, but the ongoing maintenance requirements, increased risk of operational issues, and potential loss of business due to driver preference can offset those initial savings.
Conclusion
The parking surface type should be a top consideration for any truck yard operator looking to attract and retain drivers. While factors like location and pricing are important, the choice between asphalt and gravel can make or break the success of your facility.
Asphalt-paved lots consistently outperform gravel surfaces, offering drivers a smoother, more organized, and more secure parking experience. By investing in the right surface, you can improve occupancy rates, boost customer satisfaction, and ultimately drive greater profitability for your truck parking business.
If you have more questions about the cost of building a truck parking facility or other operational considerations, don’t hesitate to reach out to the Rig Hut team. We’re here to help you transform your underutilized land into a thriving, driver-friendly truck parking operation.